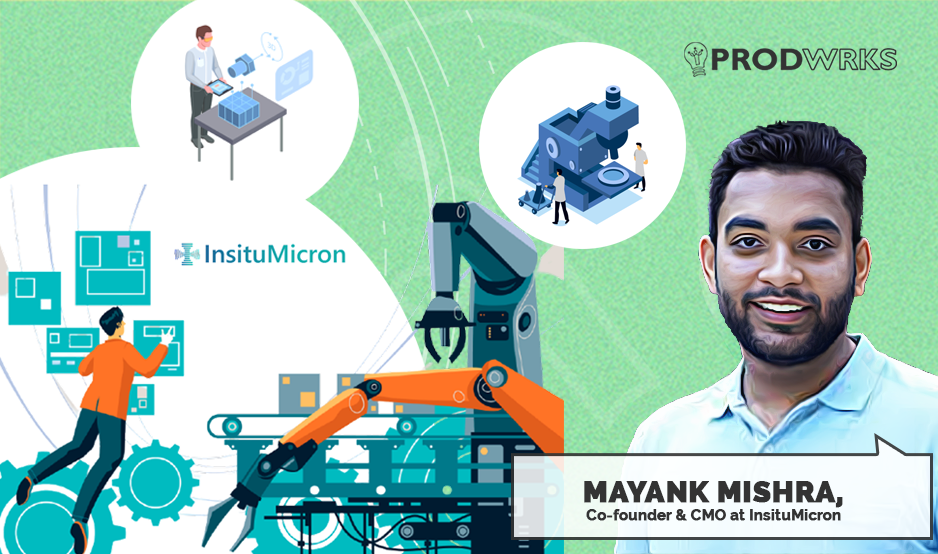
“Companies importing materials into India price their equipment so high that the gap between what academic institutions can typically spend and what these machines cost is massive,” says Mayank Mishra, Co-founder of InSitu Micron. “Researchers often have to write large grant proposals just to raise enough funds to afford them.”
“That made me think,” he says. “If a premium institute like IIT Madras had to struggle this much, what would it be like for smaller universities?”
This became the starting point for InSitu Micron, a compact scientific material testing instrument designed for small-scale testing. Their machines can be integrated directly into microscopes or X-ray systems, allowing real-time, in situ testing of materials at a microscopic level.
Founded by Kousik Papakollu, Lalith Kumar Bhaskar, and Mayank Mishra, InSitu Micron is based in Chennai. In this story, we uncover how In Situ Micron is tackling the barriers to material testing in Indian research.
How a Research Roadblock Sparked In-Situ Micron’s Origin
“He tried to procure it eight years ago, and at the time, they quoted around 1.1 to 1.2 crore for the same machine,” says Mayank. “It was a huge amount. We clearly couldn’t afford it, so he said it wasn’t that hard and decided to build it himself.”
Undeterred, Lalit spent the next three years building the instrument himself while continuing his research. Once it was functional, he used it for his experiments. After completing his doctoral work, he moved on to a postdoctoral position while the instrument stayed behind as a working prototype that would eventually lay the foundation for InSitu Micron.
When Mayank joined IIT Madras as a researcher, Introducing the instrument into the market was never the plan. That changed when a colleague pointed out that if even IIT Madras had struggled to afford it, what hope did smaller colleges have? That question pushed them to take it to market.
Mayank explains, “We did some market research, spoke to professors and industry folks, and realized that with a few tweaks, the instrument could become a viable product with real demand. That’s how we got started.”
Building Compact Tools for Deeper, In-Situ Material Testing
“When we talked to people, they were interested in doing such a thing,” he said. “That also kind of gave us validation that if we could come up with something like that, there were people who are ready to buy it.”
Mechanical testing had long been part of materials research, but the machines used for it were bulky and demanding. They required large samples, which became a major constraint when dealing with costly or experimental materials. For many researchers, the high material requirement was enough to steer them away from deeper research into expensive materials
The machines built at In-Situ Micron aim to address that problem. By reducing the size of both the equipment and the required sample, the team created a system that could deliver the same test results with less material. In-Situ Micron’s system also outputs the raw data in formats like Excel, along with the plotted stress-strain graph, a crucial tool for researchers.
Mayank says, “If you're working with costly materials like rare earths or gold-doped samples, you usually need 500 grams to a kilo for testing. That made people hesitant to explore new materials. That is where our machine helps. It gives the same results using much smaller samples.”
“These are existing tools,” Mayank says. “The optical microscope is already there, the X-ray diffractometer is already there. What we are doing is placing our instrument inside those systems. It is that small. That is what in situ means. That is how we arrived at the name In-Situ Micron.”
A Research Tool Built for Range and Depth
“You can see what’s happening at a much deeper level,” Mayank said. “It’s not just about when a material breaks, but how it behaves under load.”
“Instead of switching between machines, everything can be done in a single setup,” he said. “It simplifies the process, especially when lab space is limited.”
Tapping Into Industry Demand for Material and Failure Analysis
Mayank explains, “We realized that if we kept academia as our primary focus, the market would eventually get saturated. If we’re building an instrument with a lifespan of 10 to 15 years, and only around 50 institutes in India are actively involved in materials research, there’s a limit to how much we can grow in that segment.”
“So industries like biomedical, aerospace, and automobile are our three major focus areas,” Mayank said. “In all of these, failure analysis is a significant need, and they can rely on the setup we’re building to support that.”
Building Reliability into Indian-Made Scientific Equipment
“There weren’t many trustworthy companies that could deliver the same quality of data or results as the German and American ones,” Mayank says. “We faced that issue ourselves, and when we spoke to others, it was clear everyone was dealing with the same problem.”
“The load cell is one of the most important sensors in any mechanical testing equipment,” Mayank explains. “Indian manufacturers were using Chinese load cells, which aren’t as reliable. We went with HBK, a well-known German company. It’s more expensive, but it gives us the reliability we need.”
“We didn’t go for the highest-end parts, but we picked what was reasonable and far more reliable than the Chinese options,” he says. “There’s nothing in our equipment that’s Chinese because we didn’t want anything that could compromise performance.”
Pricing Built Around Flexibility and Use Case
In-Situ Micron sells two core machines. The uniaxial system is priced between ₹15 and ₹25 lakh, depending on the configuration. The biaxial version, which supports more complex testing, ranges from ₹40 to ₹50 lakh.
The price varies based on what is included. Features like digital image correlation (DIC), higher-resolution sensors, or more precise load cells push the price upward. At the lower end, labs can opt out of those features and still get reliable data, just with fewer decimal points and less granularity.
Beyond the base systems, the company also offers add-on modules tailored to specific environments. A high-temperature module can add ₹10 to ₹15 lakh to the total cost. Cryogenic modules are in the same range. Corrosion-testing setups are the most expensive, sometimes adding ₹20 to ₹25 lakh on top.
“We looked at how much time it saves, how much expertise is needed to run it, and what it replaces,” Mayank said. The goal was to factor in the practical value, not just the hardware. If a machine could be operated by someone without specialized training, that alone would reduce overhead for labs and that mattered to us”
Building with Constraints, Learning on the Fly
“We didn’t have the funds to hire specialists, so we focused our limited resources on R&D rather than salaries,” Mayank said. That meant learning a lot on our own, especially outside our core expertise”
Features and Simplifying Use Based on Real-World Needs
“Bi-axial was closer to how materials are used,” Mayank explained, “but we saw that there wasn’t much interest in it. For quality checks and research purposes, most people preferred uniaxial testing.”
To reduce reliance on service teams and cut down long lead times, In-Situ Micron designed its machines to be easy to install and maintain. Research labs could handle the setup themselves, and in cases of breakdown or downtime, users were able to perform basic diagnostics without having to wait for external support.
Insitu Micron also responded to feedback around software complexity. In many research labs and industrial settings, users often rotate, making repeated training impractical. To address this, the team rebuilt the software to be simple and intuitive, easy enough for someone to operate even on their first use.
“In research labs and even in industry, people come and go. No one stays long enough for repeated training,” he said. “Everyone wanted software that was easy to use, and we kept that in mind while building it.”
Automating Prediction and Failure Analysis in Materials Testing
“We’re building models that predict mechanical properties before the test even starts, which would be useful in both academia and industry.”